Products
Colding Heading Dies Tungsten Carbide Molds
Five Advantages Of Products
- Carbide finished product mold
- drawing mold/bushing
- Per your requirement,customised
- Customer Size Accepted
- 100% pure tungsten Carbide
Product Details
Product Description
The cemented carbide cold heading die is required to have good impact toughness, fracture toughness, fatigue strength, bending strength, and wear resistance under the wear-resistant working condition of impact or strong impact.
Tungsten Carbide Cold Heading Dies Characteristics:
1. High wear resistance. Tungsten carbide cold heading dies material high wear resistance, tensile modulus can be guaranteed long-term work in any degree of deformation, ensuring standard size unchanged.
2. Excellent in polishing. Carbide has a good polishing, can be processed into the die hole mirror light, ensuring high quality standard surface.
3. Adhesion to metal is small. In the tungsten carbide cold heading process, ferrous metal material adhesion small carbide tooling materials, ensuring a high tungsten carbide cold heading die life.
4. The friction coefficient and energy consumption is small.
5. High thermal conductivity. Since the thermal conductivity of the tungsten carbide die is high, heat generated during the cold forging can quickly conducted away to improve the durability of the mold.
6. Good corrosion resistance.
BENEFITS OF TUNGSTEN CARBIDE IN TOOLING
Strength – Tungsten carbide has very high strength for a material and is extremely hard and rigid. Compressive strength is higher than almost all melted, cast, forged metals and alloys.
Rigidity – Tungsten carbide compositions range from (2) to (3) times as rigid as steel and (4) to (6) times as rigid as cast iron and brass. Young’s Modulus is up to 94,800,000 psi.
Heat Resistance – Tungsten Carbide is highly resistance to deformation and deflection and is very valuable in applications where a combination of minimum deflection and good ultimate strength is the first consideration.
Impact Resistant – For such a hard material with very high rigidity, the impact resistance is high.
Heat and oxidation resistance – Tungsten-base carbides perform well up to about 1000°F in oxidizing atmospheres and to 1500°F in non-oxidizing atmospheres
Low temperature resistance (cryogenic properties) – Tungsten carbide retains toughness and impact strength in the cryogenic temperature ranges. (-453°F.)
Thermal Conductivity – Tungsten carbide is in the range of twice that of tool steel and carbon steel.
Electrical Conductivity – Tungsten carbide is in the range equal to that of tool steel and carbon steel.
Specified Heat – Tungsten carbide ranges from about 50% to 70% as high as carbon steel.
Weight – The specific gravity of tungsten carbide is from 1-1/2 to 2 times that of carbon steel.
Hot Hardness – When temperature increases to 1400°F, tungsten carbide retains much of its room temperature hardness. At 1400°F, some grades equal the hardness of steels at room temperature.
Tolerances – Many surfaces or even complete parts can be used the way they come from the furnace, “as sintered”, such as mining or drilling compacts. In those parts requiring precision ground accuracy, such as stamping dies, close-tolerance preforms are provided for grinding or EDM.
Methods of Fastening – Tungsten carbide can be fastened to other materials by brazing, epoxy cementing or mechanical means. Tungsten carbide’s low thermal expansion rate must be carefully considered when preforms are provided for grinding or EDM.
Coefficient of Friction – Tungsten carbide compositions exhibit low dry coefficient of friction values as compared to steels.
Galling – Tungsten carbide compositions have exceptional resistance to galling and welding at the surface.
Corrosion-Wear Resistance – Specific grades are available with corrosion resistance approaching that of noble metals. Conventional grades have sufficient resistance to corrosion-wear conditions for many applications.
Wear-Resistance – Tungsten carbide wears up to 100 times longer than steel in conditions including abrasion, erosion and galling. Wear-resistance of tungsten carbide is better than that of wear-resistance tool steels.
Surface Finishes – Finish of an as-sintered part will be about 50 micro inches. Surface, cylindrical or internal grinding with diamond wheel will produce 18 micro inches or better and can produce as low as 4 to 8 micro inches. Diamond lapping and honing can produce 2 micro inches and with polishing as low as 1/2 micro inch.
MiXiao Tech
Contact Person: Michelle
Telephone: +86 13650157503
Landline: +86 13650157503
Company Address: Chang’.an Town,Dongguan City,Guangdong Province,China
Factory Address: Jinxia Industrial Zone,Chang’an Town,Dongguan City,Guangdong Province,China
Website: mixiao.us764.com
Previous: Powder Mold Metallurgy Compacting...
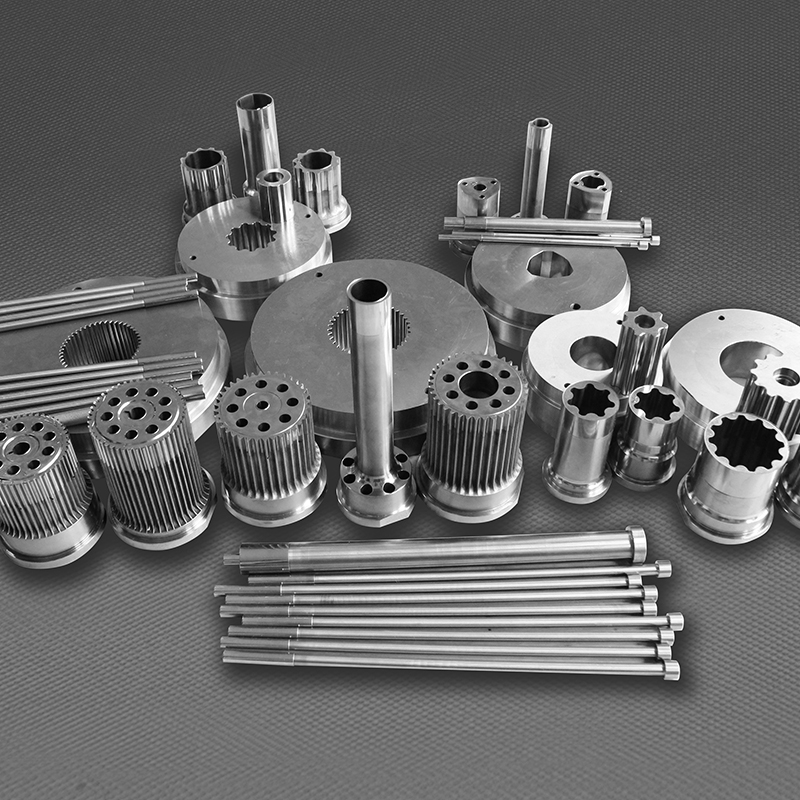
Powder Mold Metallurgy Compacting Dies Tooling
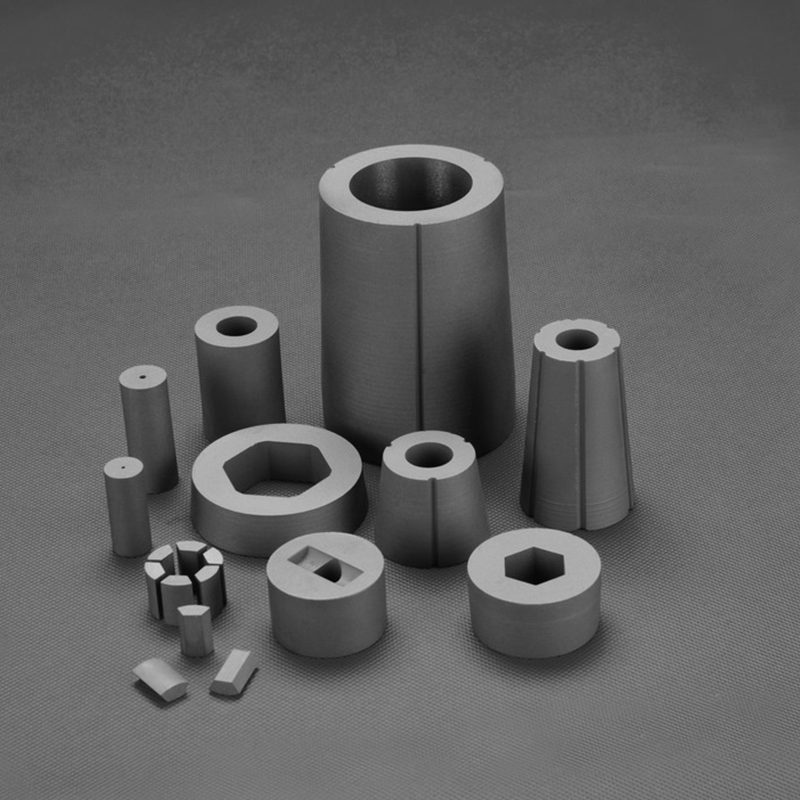
Colding Heading Dies Tungsten Carbide Molds
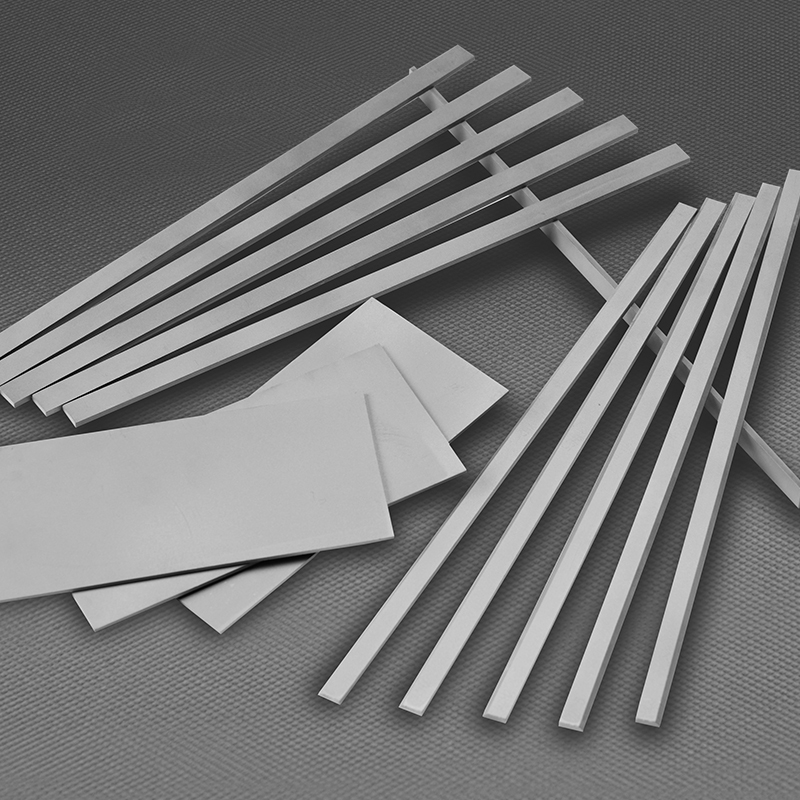
Cemented Tungsten Carbide Strips Bar
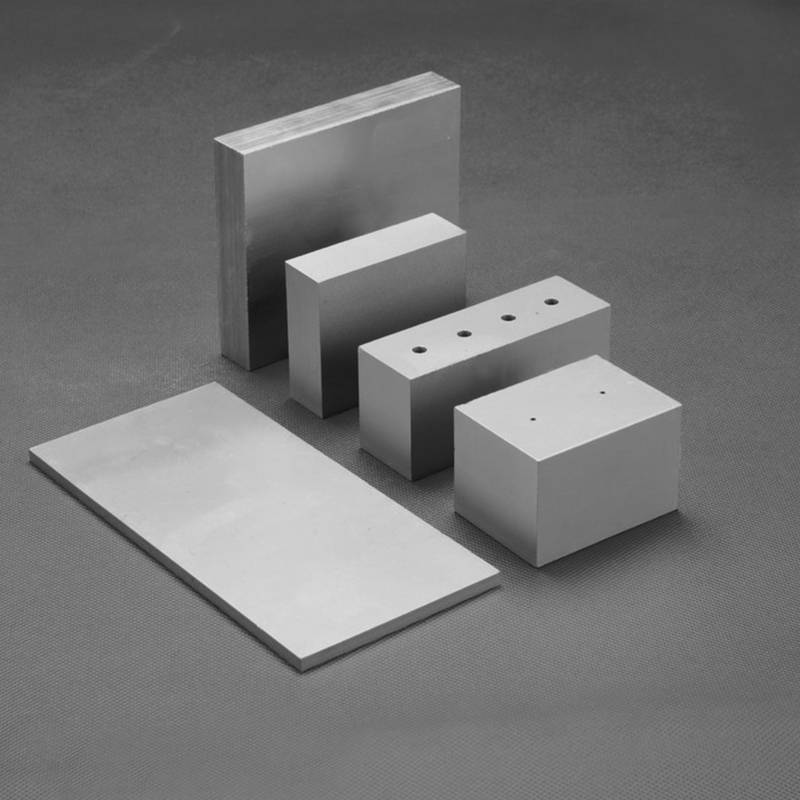
Tungsten Carbide Block Plate Strips
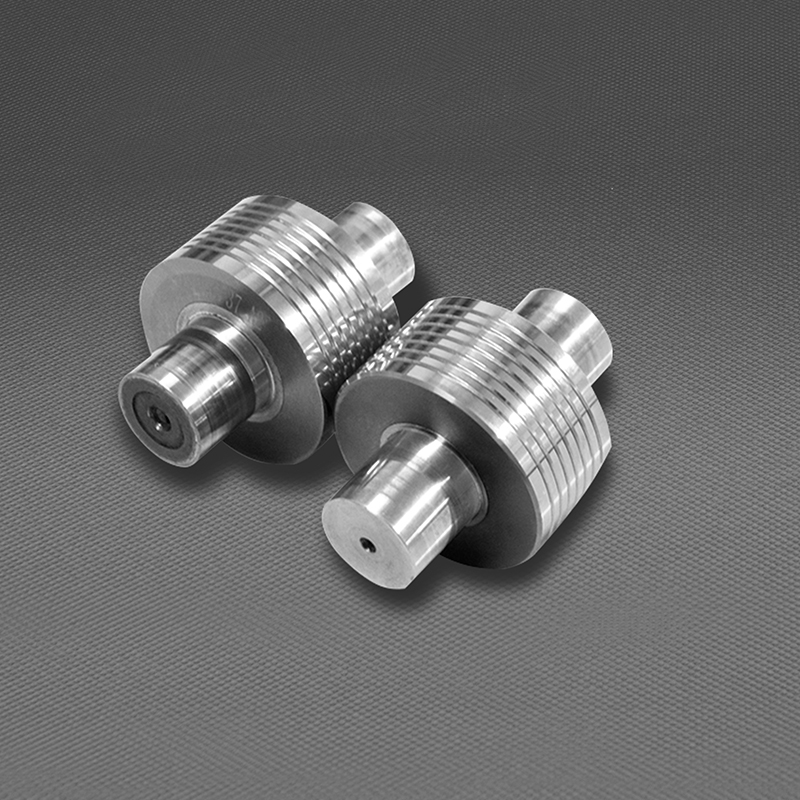
Tungsten Carbide Precision Rolls
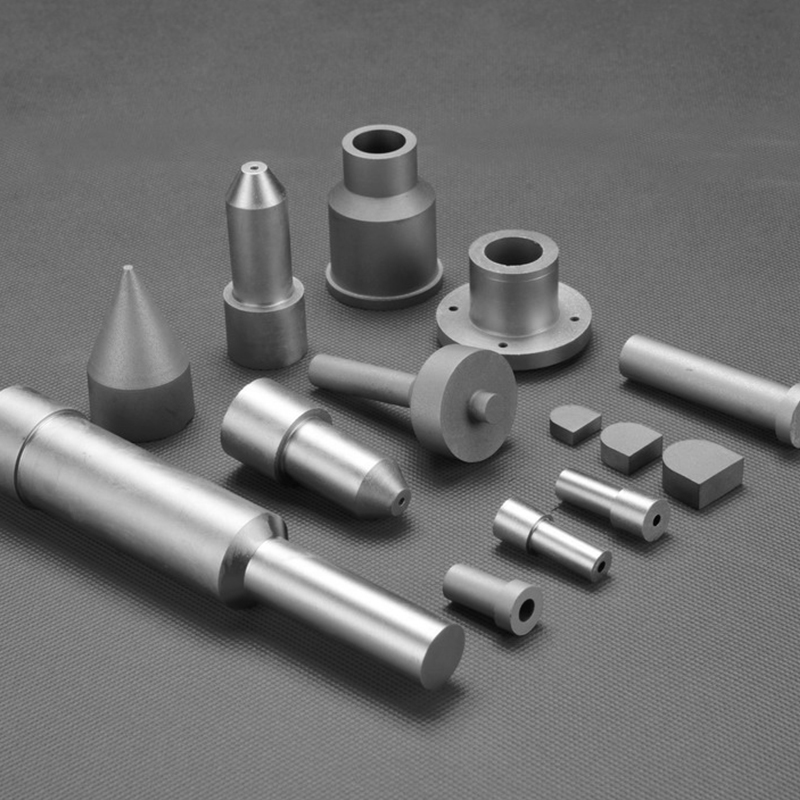
Wear-Resistant Mold Blanks
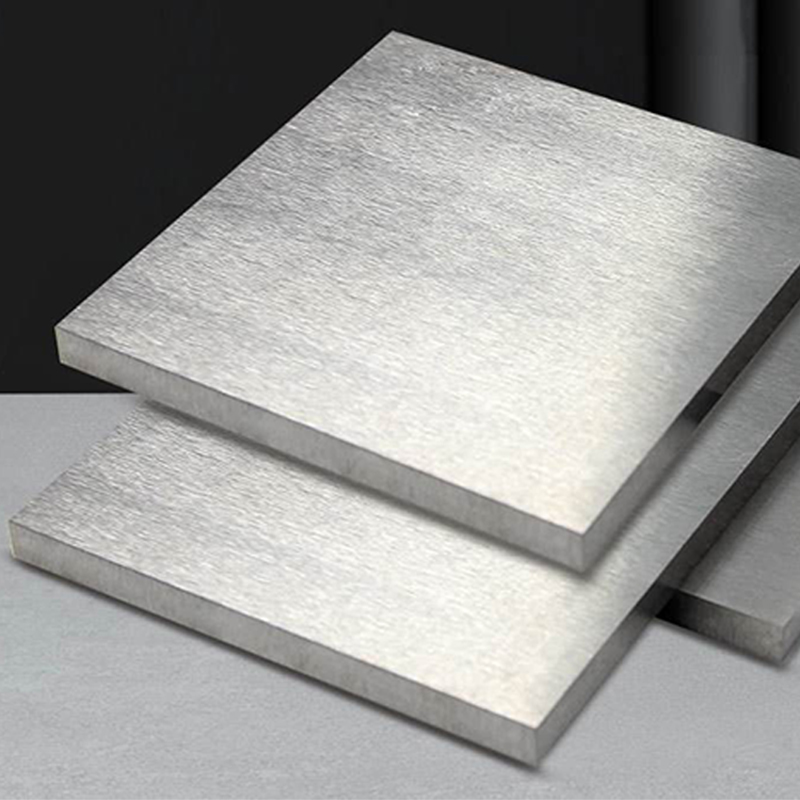
Tungsten Carbide Punches Plates Cemented Sheet
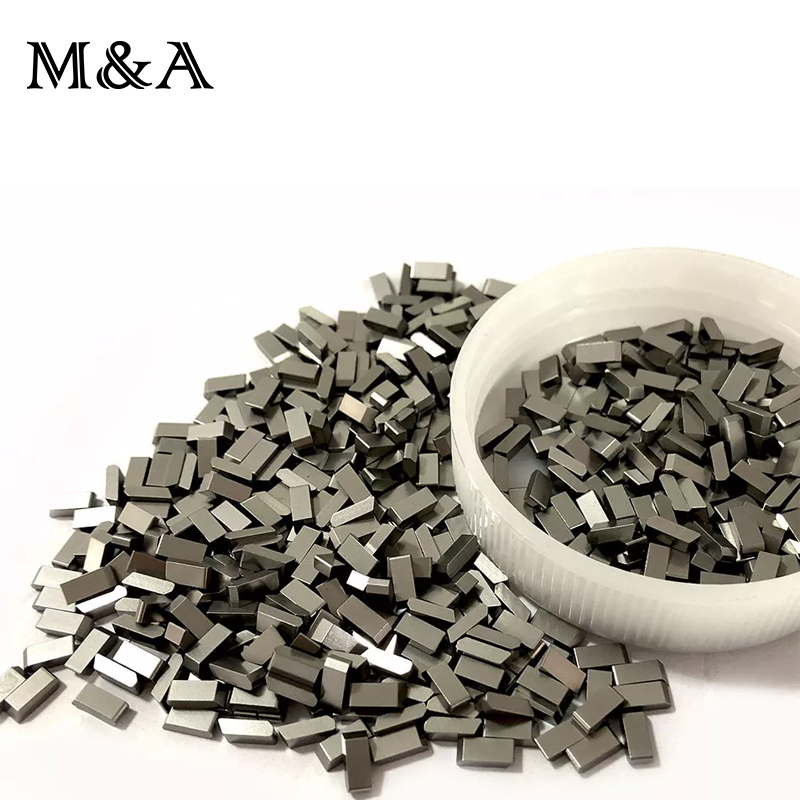